Welding Technology . Transforming the Future of Fabrication
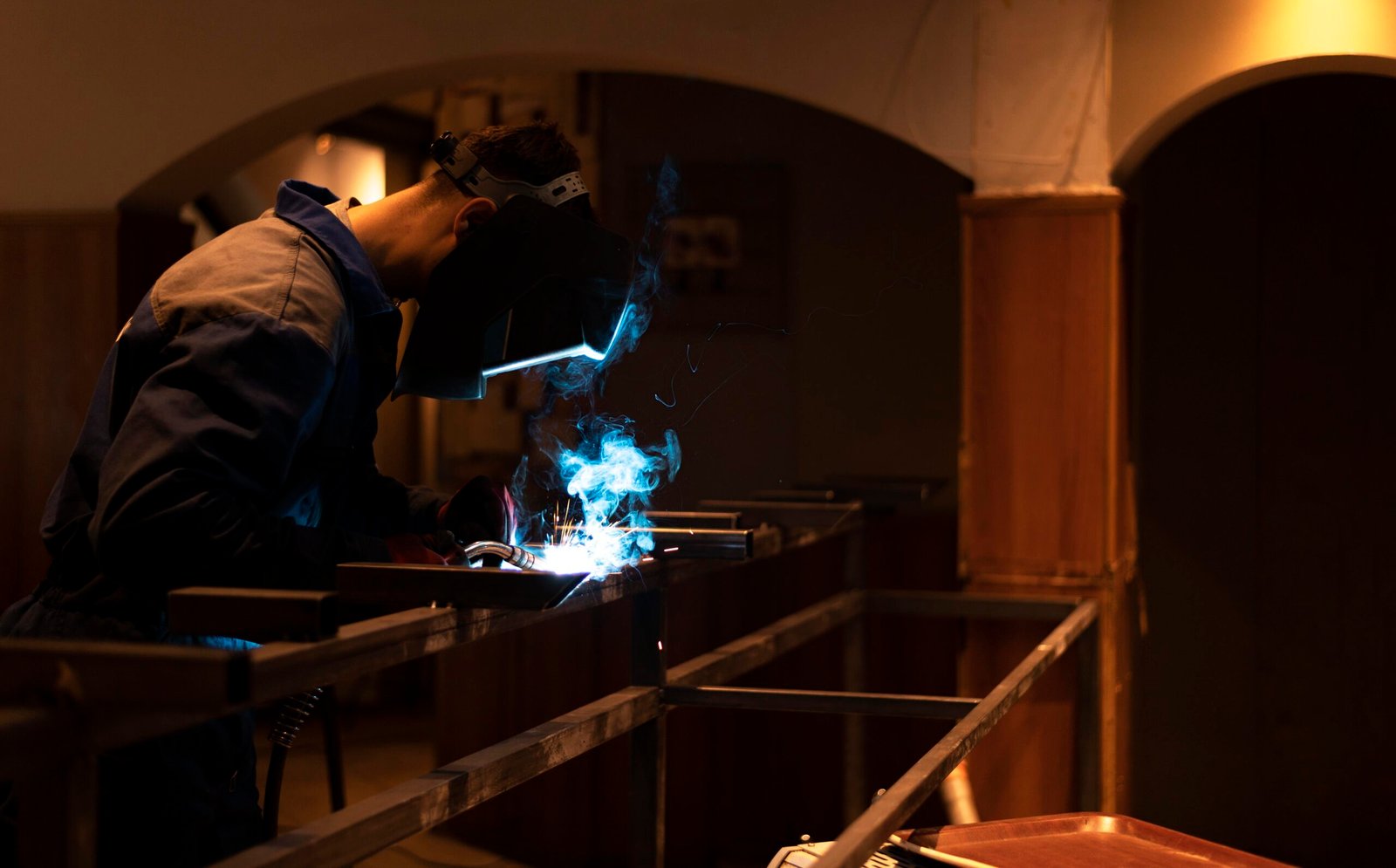
The foundation of the metal fabrication sector is welding technology, which lets us unite components essential in many other sectors and assemble buildings. From automotive to aerospace, welding technology is always developing and satisfying needs for accuracy and efficiency. The development of welding technology, its present uses, needs, and upcoming developments are investigated in this paper.
1. Introduction to Welding Technology
Welding is the process of melting the basic materials and adding filler material to combine metals—and occasionally thermoplastics. What ties bridges, autos, towers, and aircraft together? Technology of Welding From a manual ability, welding has evolved over time into a tech-driven sector heavily dependent on robotics, laser, and automation.
Welding Engineer Dr. John Smith notes, “The constant evolution of welding technology not only enhances our ability to join metals but also transforms how industries fabricate and innovate.”
2. Evolution of Welding Technology
From the Bronze Age, welding has existed; early advancements concentrated on simple heat and pressure methods. By means of developments like arc welding and resistance welding, fast forward to the 20th century and industry practices adopted these standards.
Welding technology advanced significantly by including computer-assisted techniques including laser welding, friction stir welding, and plasma cutting by the twenty-first century. By guaranteeing more precision, more effective energy consumption, and more strong weld strength, these contemporary techniques have transformed sectors.
3. Current State of Welding Technology
Welding technology nowadays consists in both conventional and automated methods. Particularly automation is reinventing mass production of fabrication to guarantee consistency and lower human error. Important techniques consist in:
- Laser Welding
Concentrated light energy in laser welding fuses metal. Its accuracy makes it indispensible in the medical and automotive equipment industries.
- Friction Stir Welding (FSW)
Using the heat from mechanical friction, FSW joins materials without melting them so maintaining their qualities. This makes it quite appropriate for light-weight but robust automotive and aeronautical uses.
Plasma Cutting
Metals with great fast accuracy are shaped by plasma cutting most often. It easily cuts through both ferrous and non-ferrous materials, ionising gas to produce plasma.
These technologies highlight the developments spurred by consumer needs for durability, accuracy, and sustainability as well as industry needs.
4. The Role of Welding Technology in Various Industries
Welding technology plays an integral role in various fields:
- Automotive Industry
Perfect connecting of complex car parts made possible by laser welding helps to produce lighter, more fuel-efficient cars. “Laser welding has opened out new frontiers in the automotive industry, allowing for more durable and lighter vehicles through precision joining of metals,” said Emily Chen, an automotive manufacturing specialist.
- Aerospace Sector
Aluminium alloy panels are joined in aircraft manufacture mostly using friction stir welding, which lowers flaws and increases fatigue resistance.
Construction Industry
Arc and resistance welding techniques of heavy-duty guarantee structural integrity of bridges and buildings.
Medical Technology
Laser welding lets delicate surgical equipment and implants be created with unmatched accuracy.
Each of these sectors depends on welding advances to satisfy customer needs and follow strict safety criteria.
5. Key Requirements of Modern Welding Technology
Modern welding technologies have to solve the following industry needs:
Precision
Particularly in industries like aerospace, where flaws are unacceptable, welding machines have to produce consistent, excellent welds.
Efficiency
Environmental as well as financial considerations depend on processes lowering material waste and energy usage.
- Flexibility
Like plasma cutting equipment, versatile welding systems provide bulk production capacity as well as fine detailed ability.
Safety
Advanced features such as fume extraction systems and operator controls prioritize worker safety without compromising performance.
- Adaptability
Welding technologies must integrate seamlessly into automated systems and smart factories.
6. Innovations in Welding Technology
Innovative ideas pushing the boundaries of what’s feasible keep the welding sector benefiting.
Robots for Welding Systems
AI-powered robotics have greatly reduced human involvement in dangerous surroundings, hence increasing safety and output.
Smart Welding Solutions
Constant monitoring of welding operations by IoT-enabled devices guarantees best performance by means of real-time feedback.
additive manufacturing
To create bespoke metal parts, 3D printing technology has started incorporating welding methods, therefore creating new manufacturing opportunities.
Case Study: Laser Welding in Automotive Manufacturing
One big automaker started using laser welding methods for vehicle body construction. Faster production times, better weld strength, and less material use resulting from this set a new standard for innovation-driven manufacturing.
7. Challenges and Solutions in Implementing New Welding Technologies
While technological advancements bring opportunities, they also introduce challenges:
- High Initial Costs
Modern systems require significant investment. Solution? Industry collaborations and government grants help reduce financial burdens for smaller businesses.
- Skilled Workforce Shortage
Advanced technologies necessitate specialized training. Solution? Partnerships with technical schools and certification programs can close the skill gap.
- Resistance to Change
Long-established companies may hesitate to adopt new technologies. Solution? Pilot programs demonstrating ROI can alleviate concerns.
Alex Turner, a Metal Fabrication Expert, emphasizes, “Plasma cutting technology has become more efficient and precise, offering metal fabricators greater flexibility and accuracy in shaping metals for a wide range of applications.”
8. Future Trends in Welding Technology
What does the future hold for welding technology?
- Greater Automation
Fully autonomous welding robots will become the norm, driving cost efficiencies and precision.
- Sustainability Focus
Eco-friendly practices, like energy-efficient welding techniques, will dominate industry conversations.
- Advances in Materials
Nanotechnology and lightweight alloys will introduce new welding challenges—and solutions.
- Augmented Reality in Training
Innovations like AR goggles will revolutionize operator training, offering immersive and interactive learning experiences.
- Integration with Industry 4.0
AI and big data will continue to refine welding processes, resulting in enhanced productivity and minimal waste.
Michael Rivera, Aerospace Engineer, predicts, “Friction stir welding will play a central role as the aerospace industry moves towards creating more fuel-efficient and structurally sound aircraft.”
9. Conclusion and Call to Action
Welding technology has consistently redefined how industries function, driving efficiency, safety, and progress. Staying ahead in this field requires continuous learning and adaptation to new advancements.
If you’re a welder, engineering student, or metal fabrication business, mastering these technologies will provide a competitive edge. Focus on integrating modern tools like laser welding and friction stir welding while investing in skill development.
For further insight into cutting-edge welding tools and techniques, stay connected with our updates—and join the movement toward more precise, sustainable, and innovative fabrication processes. Take the next step today.
This article ensures you’re not just informed but also ready to adapt and thrive in the exciting landscape of welding technology.